Evaluating Materials: Choosing the Right Tools for Restoration
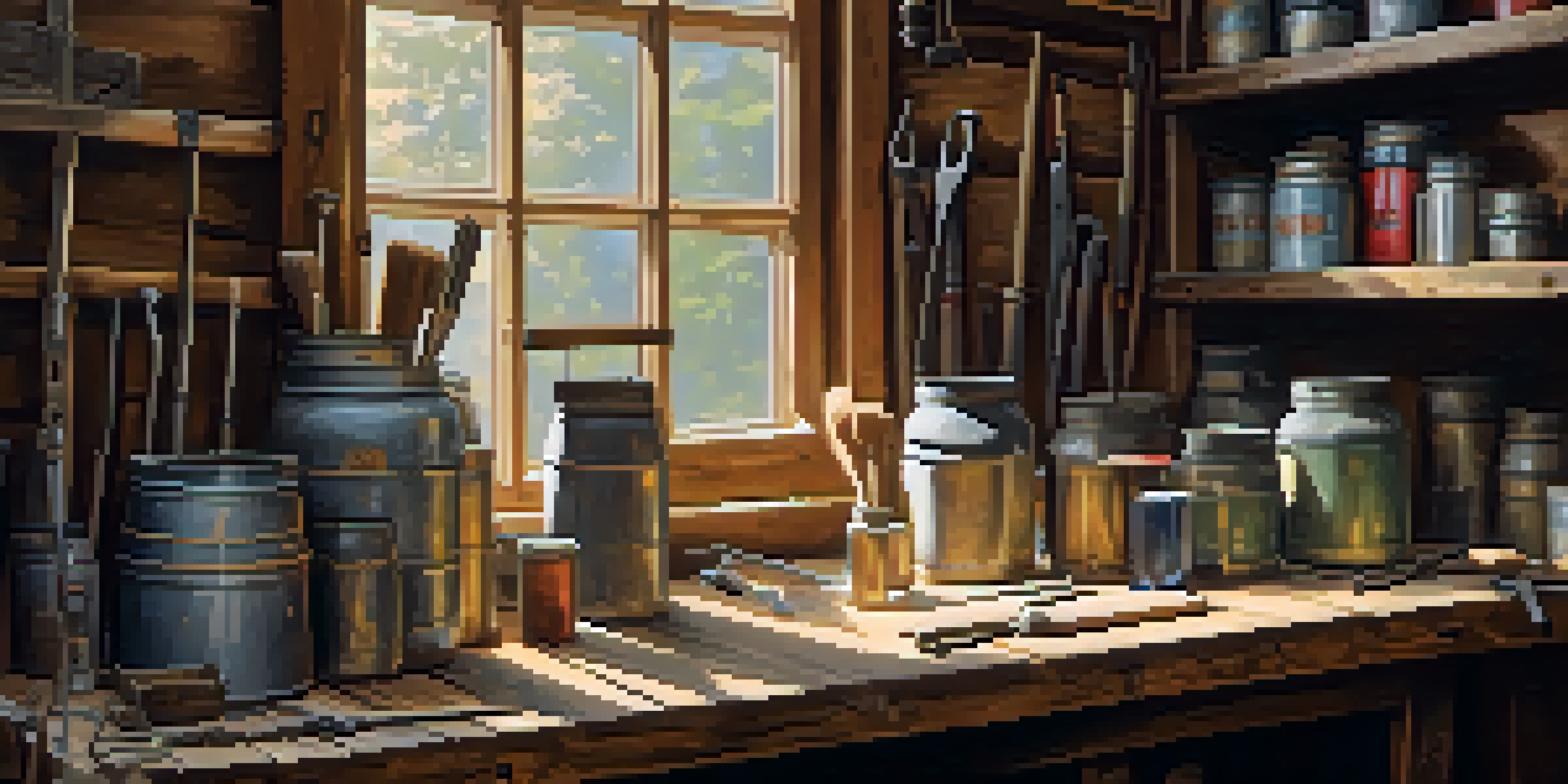
Understanding the Importance of Material Evaluation
When embarking on any restoration project, the materials you choose can make or break the outcome. Evaluating materials is essential not just for aesthetic reasons, but for durability and functionality as well. Think of it like cooking; using fresh ingredients leads to a better meal, just as high-quality materials lead to a successful restoration.
Quality is never an accident; it is always the result of intelligent effort.
Moreover, evaluating materials allows you to align the restoration with the original design and historical accuracy. This attention to detail can significantly enhance the authenticity and value of the restored item or space. Just as a chef respects traditional recipes, a restorer must honor the original craftsmanship.
In essence, the right materials not only support the integrity of the restoration but also ensure that it withstands the test of time. So, let’s delve into how to effectively evaluate and choose these materials.
Assessing the Condition of Existing Materials
Before you start sourcing new materials, it’s crucial to assess what you currently have. Evaluate existing materials for their integrity, condition, and suitability for restoration. This process is akin to a doctor diagnosing a patient; you need to understand the baseline before prescribing a treatment.
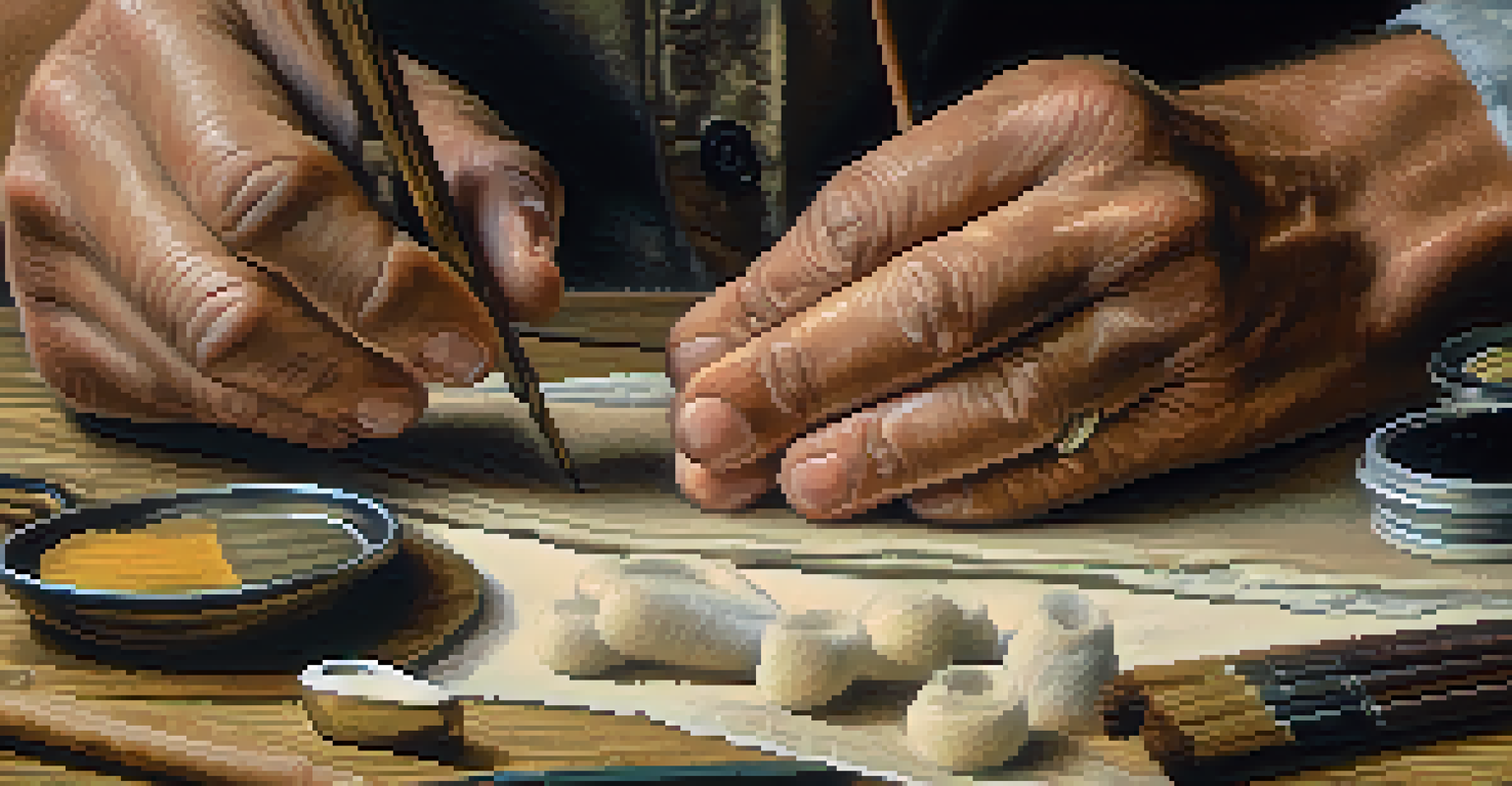
Look for signs of wear, damage, or degradation. Understanding these factors can help you determine whether to repair, replace, or reinforce existing materials. A well-informed decision can save time and resources, making the restoration smoother.
Evaluate Materials for Success
Choosing the right materials is crucial for ensuring durability, functionality, and historical accuracy in restoration projects.
By assessing the current materials, you can also gain valuable insights into historical methods and craftsmanship used in the original piece. This knowledge can guide your choices and ensure that the restored item maintains its character.
Researching Material Options and Sources
Once you've evaluated existing materials, the next step is researching potential replacements or enhancements. This stage is similar to shopping for the best ingredients; you want quality, reliability, and suitability for the task at hand. Various suppliers may offer different materials, so take the time to explore your options.
The details are not the details. They make the design.
Consider visiting local suppliers, online resources, and even specialty shops that cater to restoration needs. Don't hesitate to reach out to experts in the field for recommendations. Their insights can prove invaluable, much like consulting a seasoned chef about secret ingredients.
Additionally, researching the properties of different materials—such as their durability, maintenance needs, and environmental impact—can help you make informed choices. A well-researched selection not only enhances the restoration but can also contribute to sustainable practices.
Evaluating Material Compatibility and Performance
Compatibility is a critical aspect of material evaluation. When selecting new materials, consider how they will interact with the existing ones. Just like a harmonious dish requires balanced flavors, successful restoration demands materials that work well together.
Test the physical and chemical properties of each material to ensure they complement each other. For instance, using a modern adhesive on a vintage wood piece may not yield the desired results. Compatibility affects not only aesthetics but also the longevity of the restoration.
Research and Test Options
Thoroughly researching and prototyping materials before use can prevent costly mistakes and enhance the quality of the restoration.
By understanding how materials behave together, you can prevent future complications and ensure a seamless restoration process. This careful evaluation will pay off in the long run, saving you from costly repairs down the road.
Considering Aesthetic and Historical Accuracy
Aesthetic appeal plays a significant role in restoration, but it should never overshadow historical accuracy. Striking a balance between these two aspects is essential. Imagine restoring a classic car; using original parts preserves its authenticity while ensuring it looks stunning.
Research the historical context of the item or space you are restoring. This includes understanding the materials that were commonly used during that period. By staying true to the original design, you honor the craftsmanship and cultural significance of the piece.
Remember, the goal is not just to make something visually appealing; it’s about telling a story through materials. When you respect this narrative, your restoration will resonate with both history buffs and casual admirers alike.
Understanding Budget Constraints and Material Costs
Budgeting is an unavoidable aspect of any restoration project, and material costs can significantly impact your overall expenses. It’s crucial to have a clear budget in place before diving into material selection. Think of it as setting a spending limit before going grocery shopping to avoid overspending.
While it’s tempting to go for the cheapest option, remember that quality often comes at a price. Investing in higher-quality materials may reduce the need for future repairs, ultimately saving you money in the long run. Like a wise shopper, weigh the pros and cons of your options before making a decision.
Balance Cost and Quality
While sticking to a budget is important, investing in high-quality materials can save money in the long run by reducing the need for repairs.
Additionally, explore alternative materials or local suppliers that may offer competitive prices. Sometimes, a little creativity can lead to substantial savings without compromising the quality or integrity of your restoration.
Testing and Prototyping Materials Before Use
Before committing to a material, testing and prototyping are essential steps. Consider this process similar to a dress rehearsal before the big performance; it ensures everything works as intended. By testing materials, you can identify any issues that may arise during the restoration process.
Conduct small-scale tests or prototypes to gauge how the materials perform under various conditions. This could involve checking adhesion, durability, or even visual appeal. The more you understand about your materials before the actual restoration, the smoother the process will go.
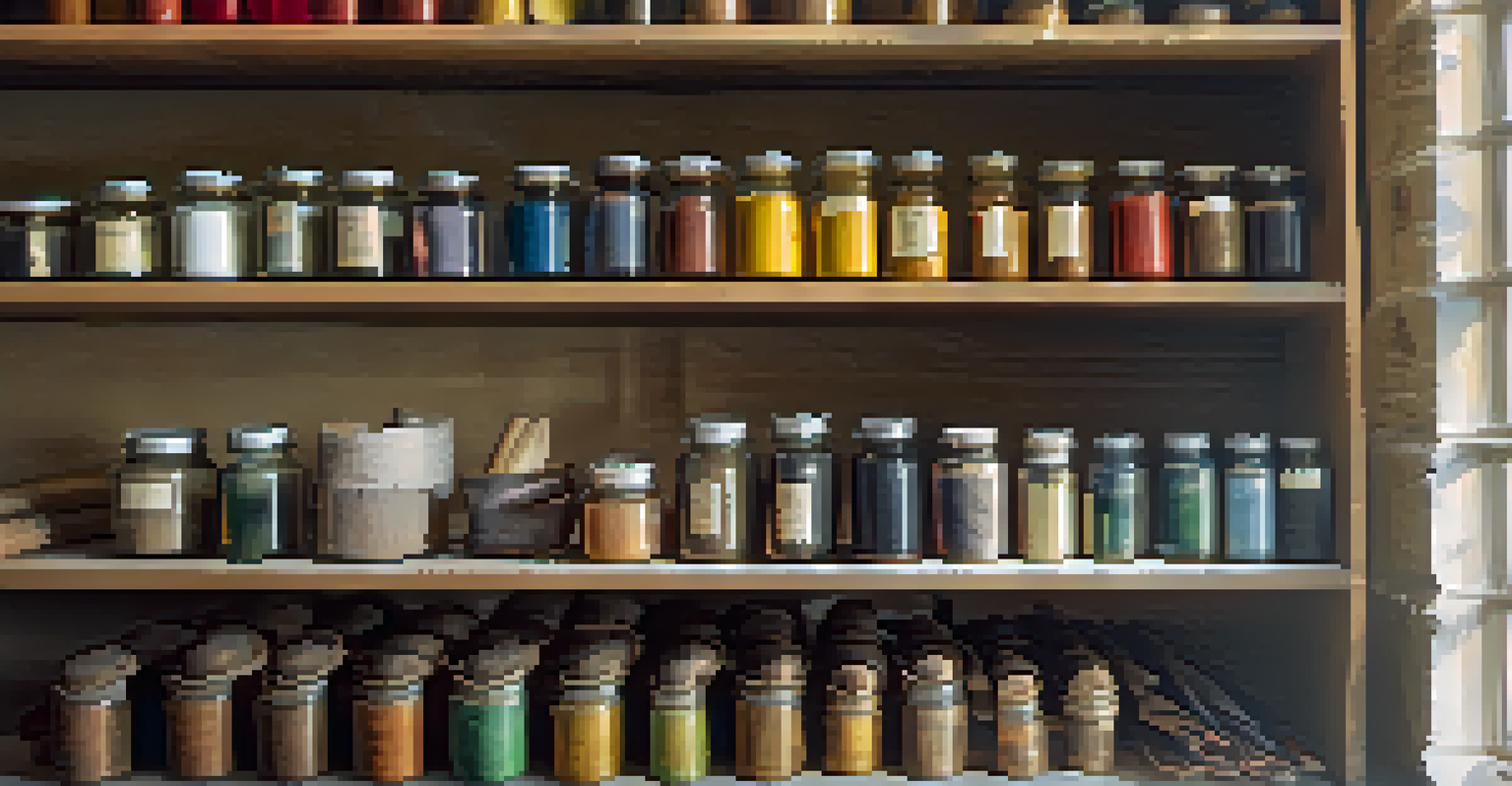
Testing not only builds confidence in your choices but also allows for adjustments before the final application. This proactive approach helps prevent costly mistakes and enhances the overall quality of the restoration.